Digital Transformation in Manufacturing: Benefits & Examples 2025
Digital transformation in manufacturing is becoming a core requirement for survival in today’s fast-evolving industrial landscape. As manufacturers face increasing pressure to reduce costs, improve efficiency, and respond faster to market demands, digital technologies are emerging as the key to driving innovation and operational excellence.
In this blog, we’ll explore what digital transformation means for the manufacturing industry, the technologies enabling it, and real-world examples of how factories are becoming smarter, faster, and more connected. Let’s scroll down!
Table of Contents
- What is Digital Transformation in Manufacturing?
- Why Digitalization Matters for Manufacturers
- Key Technologies in Digital Manufacturing
- Examples of Digital Transformation in Manufacturing
- Challenges in Digitalization
- Smart Manufacturing Solutions of Kaopiz
- Conclusion
- FAQs
What is Digital Transformation in Manufacturing?
Digital transformation in manufacturing is the full transition to integrate modern digital technologies into every part of the manufacturing value chain to improve operations, increase efficiency, and drive innovation. This reform can be implemented all at once or gradually, depending on the organization’s goals and resources.
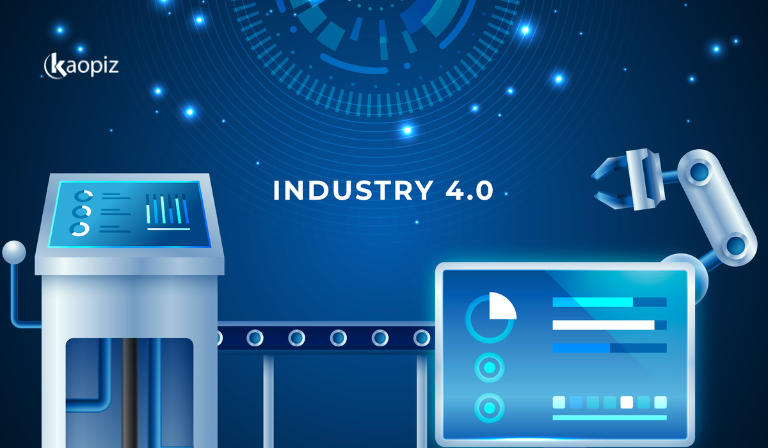
The key drivers of this shift include software applications, data digitization, and automation technologies. From mobile apps that support frontline workers to robotic process automation (RPA), ERP systems, and even 3D printing, each tool contributes to a smarter, more agile manufacturing environment. The core focus areas are operational efficiency, improved customer experiences, and leveraging big data for better decision-making.
Why Digitalization Matters for Manufacturers
Staying competitive means more than boosting production speed – it requires embracing digital tools that drive smarter decisions, greater efficiency, and innovation. Let’s explore why digitalization in manufacturing has become a solid business imperative, not just a technological upgrade.
Operational Efficiency
One of the most immediate and impactful benefits of digital transformation in manufacturing is improved operational efficiency. By automating routine tasks, digitizing workflows, and enabling real-time monitoring, manufacturers can significantly reduce downtime, waste, and manual effort.
Technologies like IoT sensors, machine learning algorithms, and centralized production dashboards help optimize everything from equipment maintenance to resource allocation. This results in faster production cycles, higher output consistency, and better utilization of both machines and manpower, ultimately creating a leaner, more agile operation.
Data-driven Decision-making
Modern manufacturing generates massive amounts of data, from production lines and supply chains to customer orders and equipment performance. Digital transformation in manufacturing allows companies to harness this data through advanced analytics and AI-powered insights, turning raw information into actionable strategies.
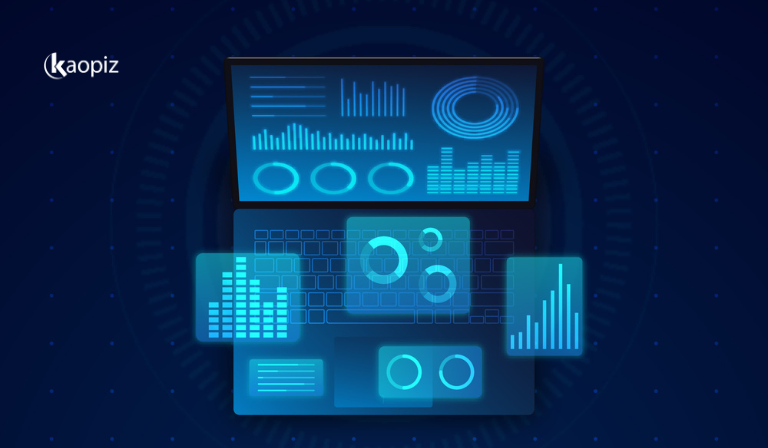
With real-time dashboards, predictive analytics, and intelligent reporting tools, manufacturers can quickly identify trends, detect inefficiencies, and make smarter decisions across operations. Data-driven manufacturing leads to faster, more confident, and more profitable decision-making. It adjusts production schedules based on demand forecasts or optimizes energy usage on the factory floor.
Cost Reduction
Implementing factory digital transformation can reduce operational costs. By automating repetitive tasks, optimizing resource usage, and minimizing downtime through predictive maintenance, manufacturers can lower both direct and indirect expenses across the production lifecycle.
Technologies like robotics, AI-driven scheduling, and digital inventory management reduce labor costs, prevent overproduction, and decrease material waste. Additionally, real-time monitoring systems help detect inefficiencies early, preventing costly disruptions and repairs. Over time, these improvements contribute to leaner operations and higher profitability.
Predictive Maintenance
Predictive maintenance is a standout benefit of digital transformation in manufacturing industry, helping companies shift from reactive to proactive equipment management. By leveraging IoT sensors, AI, and real-time data analytics, manufacturers can monitor the condition of machinery continuously and predict failures before they happen.
Instead of waiting for a breakdown or relying on fixed maintenance schedules, predictive maintenance analyzes patterns, such as vibration, temperature, or energy consumption, to detect early warning signs of wear and tear. This reduces unplanned downtime, extends asset lifespan, and cuts repair costs significantly.
Supply Chain Visibility
In a global manufacturing environment, having clear visibility into every stage of the supply chain is essential. Digital transformation in manufacturing empowers businesses with real-time supply chain data, helping them track materials, shipments, and supplier performance across multiple locations.
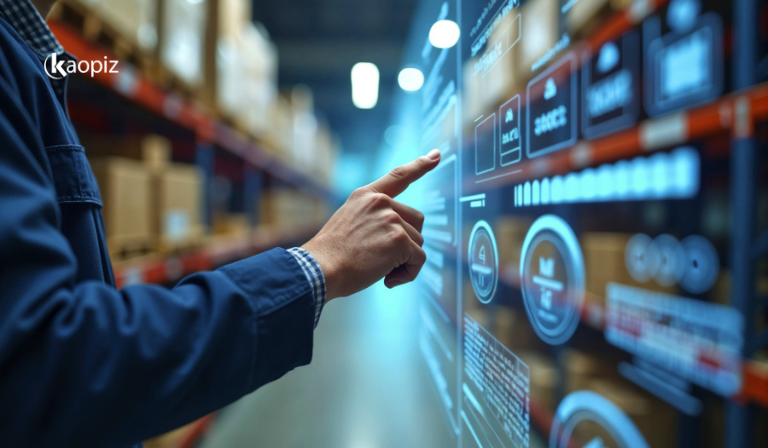
With tools like IoT-enabled tracking, cloud-based platforms, and AI-powered forecasting, manufacturers can proactively respond to disruptions, manage inventory more efficiently, and improve delivery accuracy. This level of transparency reduces delays, minimizes overstock or shortages, and builds more resilient, responsive supply chains.
Key Technologies in Digital Manufacturing
At the heart of digital transformation in the manufacturing industry are cutting-edge technologies that enable factories to become more intelligent, efficient, and connected. These innovations drive everything from predictive insights and automation to real-time decision-making and simulation.
Below are four key technologies shaping the future of smart manufacturing solutions in 2025 and beyond.
AI in Manufacturing
AI helps manufacturers process large volumes of data, optimize production processes, and automate decision-making. The algorithms can detect patterns, predict equipment failures, improve quality control, and even personalize product configurations in real time. Whether used in predictive maintenance or demand forecasting, AI in manufacturing enhances efficiency and precision across the value chain.
IoT in Manufacturing
IoT connects machines, tools, and systems through smart sensors, enabling seamless communication and data sharing across the factory floor. The devices monitor everything from temperature and pressure to production speed and machine health, allowing real-time insights and remote control. This connectivity is crucial for reducing downtime, improving safety, and enabling data-driven manufacturing automation.
Robotics and Automation
Robotics and manufacturing automation have revolutionized repetitive, high-risk, or precision-based tasks in production. From robotic arms on assembly lines to autonomous mobile robots in warehouses, automation enhances speed, consistency, and safety. When integrated with AI and IoT, robotics becomes even more powerful, enabling manufacturers to scale efficiently and respond to changes in demand with agility.
Digital Twin Technology
A digital twin is a virtual replica of a physical system, process, or product. It allows manufacturers to simulate operations, test scenarios, and monitor real-time performance without interrupting production. By combining IoT data and AI modeling, digital twins enable smarter decisions, faster problem-solving, and continuous optimization of manufacturing systems.
Examples of Digital Transformation in Manufacturing
To understand the true impact of digital transformation in manufacturing, it is necessary to look at how leading companies are applying these technologies. From smart factories to AI-powered quality control, these examples showcase how innovation is driving measurable results across the industry.
Smart Factories with Real-time Dashboards
Smart manufacturing refers to the use of digital technologies, automation, and data analytics to optimize every aspect of factory operations. A standout feature of this approach is the use of real-time dashboards, which aggregate data from connected machines and systems to give manufacturers complete visibility into performance at any given moment.
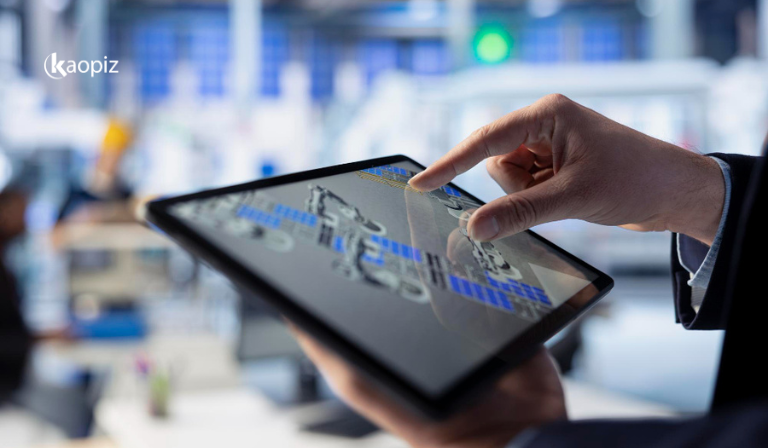
These dashboards – powered by IoT sensors, AI analytics, and cloud integration – allow teams to monitor KPIs, track machine health, and respond to issues immediately. Whether it’s adjusting production schedules, resolving bottlenecks, or managing inventory, real-time insights help drive faster, more informed decisions.
Quality Assurance Using Computer Vision
Maintaining consistent product quality is critical in manufacturing, and computer vision has become a game-changing technology in this area. By combining high-resolution cameras with AI image analysis, manufacturers can automate the inspection process, detecting defects, inconsistencies, or anomalies that might be missed by the human eye.
These systems can evaluate products in real time on the production line, flagging issues like surface flaws or dimensional inaccuracies. Over time, AI in manufacturing learns from inspection data to improve accuracy. This not only ensures higher product quality but also reduces waste, lowers recall risk, and speeds up production.
Digital Twin for Factory Simulation
A digital twin mirrors real-time data from its physical counterpart. In manufacturing, digital twins are being used to simulate entire production environments, allowing teams to visualize workflows, test scenarios, and optimize performance without interrupting actual operations.
By integrating IoT sensors, machine data, and AI-driven analytics, manufacturers can use digital twins to model factory layouts, experiment with production line changes, or predict how equipment will behave under different conditions. This enables better planning, reduced downtime, and more efficient resource allocation.
Predictive Maintenance Using Sensors and AI
Predictive maintenance is a smart maintenance strategy that uses IoT sensors and AI algorithms to monitor machinery in real time and predict when repairs or part replacements are needed, long before a breakdown occurs. It helps manufacturers move away from reactive or time-based maintenance and toward a data-driven approach.
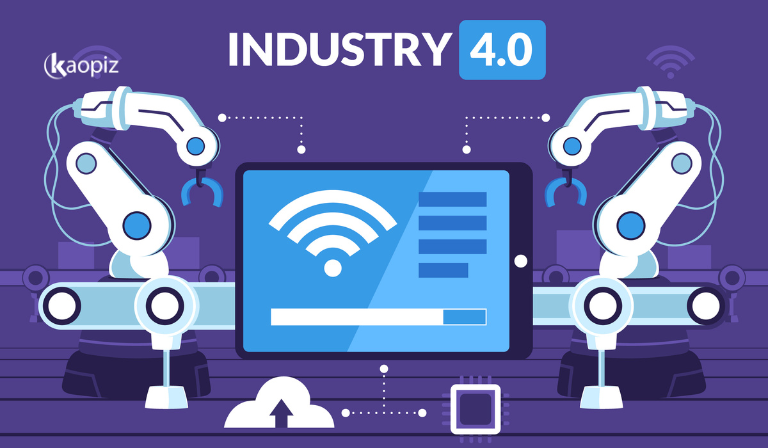
By continuously analyzing factors like vibration, temperature, and operating cycles, predictive maintenance systems detect early warning signs of wear or failure. These systems can even trigger work orders or send alerts when anomalies are detected, ensuring timely action without manual intervention.
Used across industries – from automotive and oil & gas to pharmaceuticals and manufacturing- predictive maintenance not only enhances operational efficiency but also significantly lowers long-term repair and labor costs.
Inventory and Logistics Optimization
Inventory management and logistics are core components of manufacturing. Factory digital transformation helps optimize both through automation, real-time tracking, and predictive analytics. By integrating AI, IoT, and cloud-based systems, manufacturers gain complete visibility into inventory levels and supply chain movement across global operations.
Smart systems can forecast demand, trigger automatic reordering, and optimize stock levels to avoid overstock or shortages. Meanwhile, logistics operations benefit from route optimization, real-time delivery tracking, and faster response to delays or disruptions. These innovations not only improve supply chain agility but also reduce waste, storage costs, and manual workload.
Challenges in Digitalization
While the benefits of digital transformation in manufacturing are significant, the journey isn’t without obstacles. Many manufacturers face practical and strategic challenges when adopting new technologies, especially in traditional or large-scale environments.
Here are some of the most common hurdles:
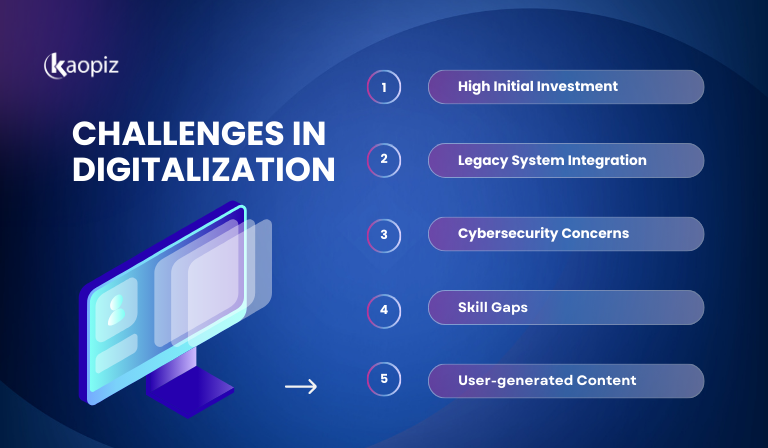
High Initial Investment
Implementing smart manufacturing software often requires significant upfront costs for hardware, software, and infrastructure upgrades. For small and mid-sized manufacturers, this can be a major barrier without a clear ROI timeline.
Legacy System Integration
Many factories still rely on outdated or fragmented systems that don’t easily integrate with modern technologies. Bridging the gap between legacy infrastructure and digital tools requires careful planning, custom development, and often costly system overhauls.
Cybersecurity Concerns
As factories become more connected, they also become more vulnerable to cyber threats. Protecting sensitive production data, customer information, and proprietary processes is critical and requires robust cybersecurity strategies and compliance frameworks.
Skill Gaps
The shift toward digital operations demands new skills in data analysis, automation, and system integration. Many manufacturers face a talent shortage or must invest heavily in upskilling their workforce to support the digital ecosystem.
Data Silos
Without a centralized data strategy, different departments or systems may collect data in isolation – creating data silos that limit visibility and hinder decision-making. Breaking down these silos is essential to unlock the full value of digital transformation.
Smart Manufacturing Solutions of Kaopiz
At Kaopiz, we help manufacturers accelerate their digital transformation by delivering tailored technology solutions that improve productivity, agility, and visibility across operations. By integrating AI, IoT, and cloud-based platforms, we enable smarter decision-making, optimized production processes, and data-driven supply chain management.
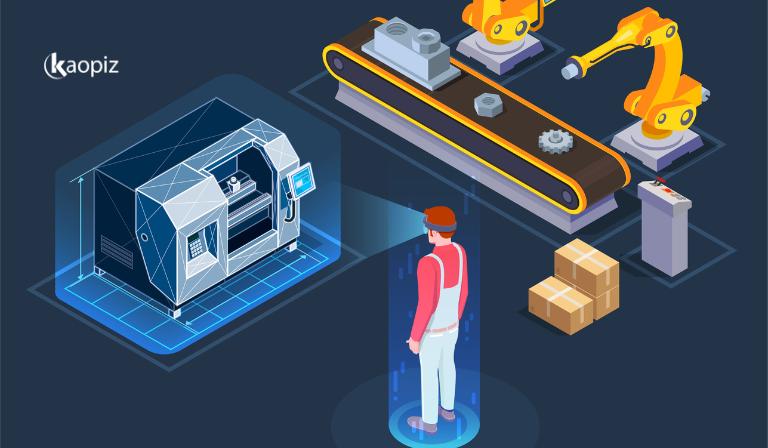
Our solutions are designed to meet the specific needs of modern manufacturers, from small factories to large-scale industrial operations, empowering them to stay competitive in the era of Industry 4.0 manufacturing.
What We Offer:
- AI-powered predictive maintenance systems: Monitor machine health in real time, reduce downtime, and extend asset lifespan with intelligent failure prediction.
- IoT-enabled factory dashboards: Gain full visibility into production lines, energy usage, and equipment performance through centralized, real-time monitoring.
- Smart inventory and logistics tracking: Automate reordering, prevent stockouts, and optimize delivery routes using AI and sensor data.
- Digital twin development: Simulate, test, and optimize factory operations with virtual replicas of physical systems to reduce risk and increase efficiency.
- Cloud-based manufacturing platforms: Connect disparate systems, break down data silos, and enable scalable collaboration between teams, departments, and partners.
Whether you’re starting your digital journey or scaling up, Kaopiz provides end-to-end support – from consulting and system integration to custom software development – ensuring your digital transformation delivers lasting impact.
Conclusion
As the factory digital manufacturing market accelerates, 4.0 transformation has become a strategic must-have for manufacturers looking to stay competitive and agile. Technologies like AI and IoT in manufacturing are reshaping operations – boosting efficiency, cutting costs, and enabling smarter, faster decisions. To fully realize these benefits, businesses need the right approach and the right partner to guide the journey.
At Kaopiz, we empower manufacturers with scalable, smart manufacturing solutions that drive meaningful transformation, helping you move faster, work smarter, and lead in a connected world.
Ready to future-proof your manufacturing business? Let’s build your smart factory together.
FAQs
What Impact Will Digital Transformation Have on Sustainability in Manufacturing?
Digital transformation helps manufacturers reduce waste, energy consumption, and emissions by enabling smarter resource management and process optimization. With tools like IoT sensors and AI-driven analytics, businesses can monitor environmental performance in real time and make data-driven decisions that support both efficiency and sustainability goals.
How Can Manufacturers Ensure Their Digital Transformation Strategy Aligns with Business Goals?
Start by defining clear objectives – whether it’s improving production efficiency, reducing downtime, or enhancing customer satisfaction. Then, align technology investments with these goals, involve cross-functional teams, and choose the right partners to support implementation and scaling. A well-aligned strategy connects digital tools directly to measurable business outcomes.
How Do I Start Digitalizing My Factory?
Begin by identifying high-impact areas, such as maintenance, inventory, or quality control, where digital tools can deliver quick wins. Assess your current infrastructure, prioritize scalable solutions like IoT, AI, and cloud platforms, and partner with a technology expert like Kaopiz to develop and execute a roadmap tailored to your needs.
Trending Post
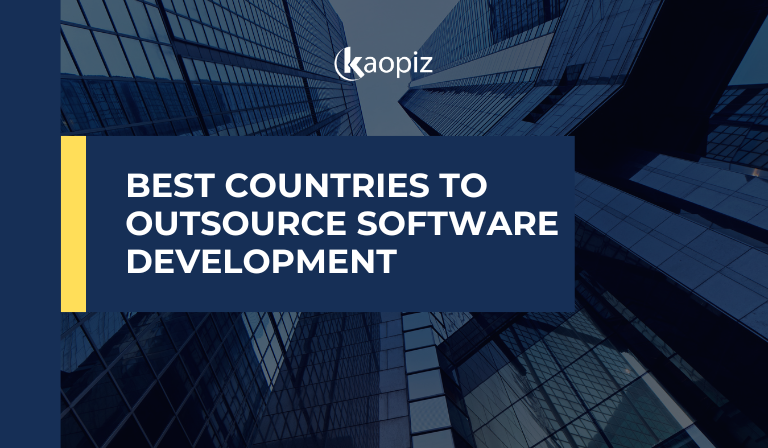


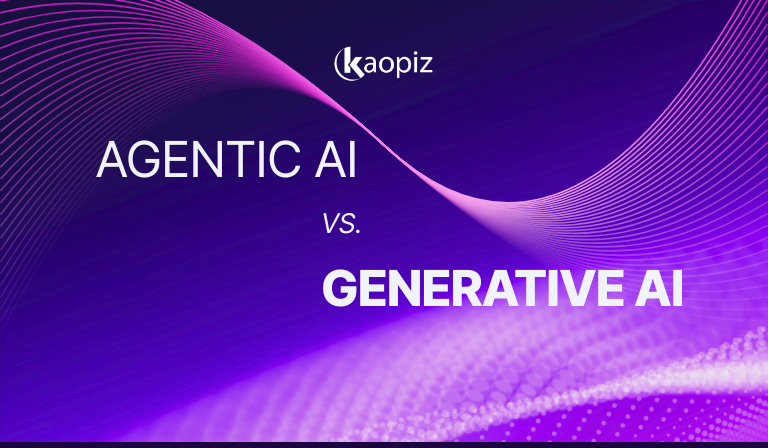