Top 10 Manufacturing IT Trends to Watch in 2025
The manufacturing industry is undergoing a rapid transformation, driven by the rise of smart technologies and the growing demand for efficiency, resilience, and sustainability. As we enter 2025, manufacturers are rethinking how they design, produce, and deliver goods – placing manufacturing IT trends at the core of their operations.
In this blog, we explore the top 10 trends to watch in 2025 – highlighting the technologies and strategies shaping the future of production and offering insights into how forward-thinking businesses can stay ahead in a competitive global landscape.
Table of Contents
- Manufacturing IT Industry Market Overview
- Top 10 Manufacturing IT Trends In 2025
- Smart Manufacturing & Industry 4.0 Evolution
- Cloud-Based Manufacturing Platforms
- Edge Computing for Faster Decision-Making
- Rise of AI & Generative AI in Manufacturing
- Advanced Robotics and Human-Robot Collaboration
- Digital Twins & Simulation Tech
- Decentralized Manufacturing
- Workforce Empowerment with AR/VR & Upskilling Tools
- Cybersecurity in Smart Factories
- Sustainability Through Green IT
- Future Outlook: What’s Next Beyond 2025?
- How Kaopiz Supports Smart Manufacturing
- Conclusion
- FAQs
Manufacturing IT Industry Market Overview
The manufacturing sector is undergoing a profound digital transformation, driven by the convergence of IT and operational technology (OT). In 2025, this shift is more pronounced than ever as manufacturers embrace advanced IT solutions to optimize production, improve resilience, and stay competitive in a volatile global market.
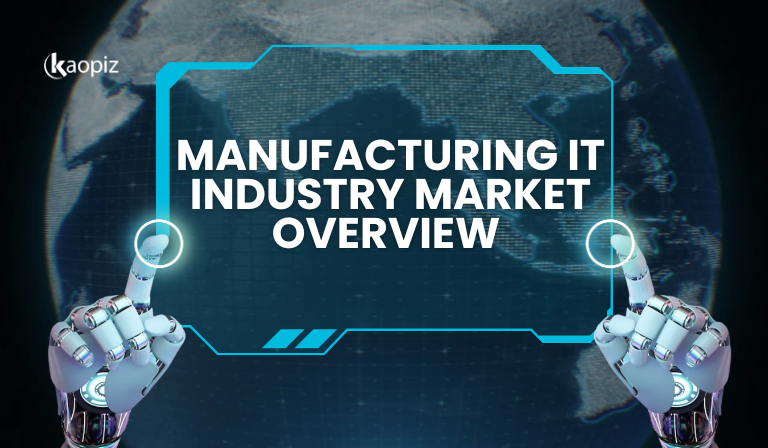
According to GlobalData, the market for enterprise IT services within the manufacturing sector was valued at $414.5 billion in 2022, and it is projected to grow at a CAGR of over 9% through 2027, reaching $642.1 billion. Similarly, the total ICT revenue opportunity in the manufacturing vertical is expected to increase from $452 billion in 2023 to more than $641 billion by 2028. This growth is driven by a combination of factors:
- Rising ICT budgets of global manufacturers
- Increased investment in 5G networks
- Expanding partnerships between manufacturers and tech startups
Looking ahead to 2025, manufacturers will continue to face a mix of opportunities and uncertainties. Elevated raw material costs, shifting policy environments post-global elections, and ongoing geopolitical tensions are contributing to a cautious outlook. For example, manufacturers surveyed in NAM’s 2024 Q3 outlook expect input costs to rise by 2.7% over the next 12 months.
In this high-stakes environment, manufacturers are doubling down on digital transformation in manufacturing to remain competitive. From AI and smart factories to decentralized production models and cybersecurity investments, IT is no longer just a support function – it’s the backbone of modern manufacturing strategy.
Top 10 Manufacturing IT Trends In 2025
Below are 10 current manufacturing IT trends that are reshaping the way products are designed, produced, and delivered.
Smart Manufacturing & Industry 4.0 Evolution
The evolution of smart manufacturing is at the heart of the modern industrial revolution, often referred to as Industry 4.0. This paradigm shift integrates cyber-physical systems, IoT, AI, and big data into every aspect of the manufacturing process, creating highly automated and intelligent production environments.
In 2025, manufacturers are moving beyond basic automation and embracing data-driven, interconnected ecosystems. Smart factories are now equipped with real-time sensors, machine learning algorithms, and predictive analytics that allow them to make autonomous decisions, optimize production lines, and reduce unplanned downtime.
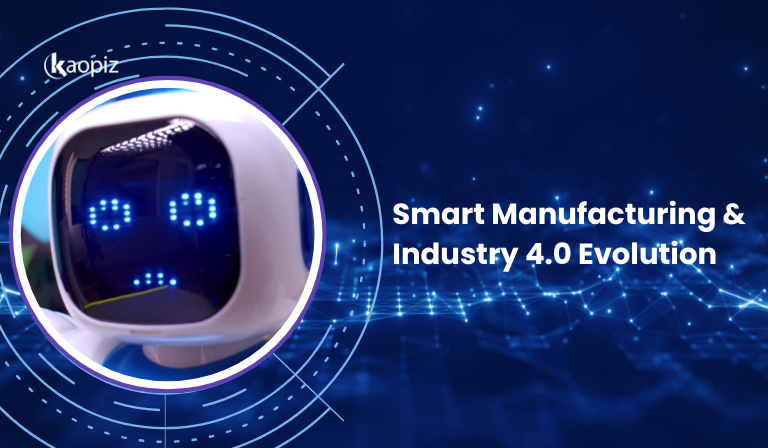
Key characteristics of smart manufacturing in 2025 include:
- End-to-end visibility across supply chains through IoT and digital twins.
- AI-powered analytics for demand forecasting, process optimization, and quality control.
- Cloud-based platforms enabling remote monitoring and decentralized operations.
- Machine-to-machine (M2M) communication driving seamless integration between systems.
Cloud-Based Manufacturing Platforms
Cloud computing has become one of manufacturing IT trends, offering scalable, flexible, and cost-effective solutions that empower businesses to operate with greater agility. In 2025, cloud-based systems will enable real-time collaboration, seamless data exchange, and centralized control across globally distributed operations.
Popular solutions include cloud-based ERP systems, smart factory platforms, and Manufacturing Execution Systems (MES) hosted on platforms like AWS, Microsoft Azure, and Google Cloud. These platforms support advanced technologies like AI, IoT, and analytics by providing the necessary infrastructure for data storage, processing, and security.
Unlike traditional on-premises systems, cloud platforms provide manufacturers with the ability to:
- Access production data remotely and make decisions in real-time.
- Integrate systems such as ERP, MES, and supply chain management across multiple locations.
- Scale resources on demand without major capital investment.
- Improve uptime and reduce maintenance with automatic updates and remote diagnostics.
Edge Computing for Faster Decision-Making
As smart factories become more connected and data-intensive, manufacturers are turning to edge computing to reduce latency and enable real-time decision-making. Unlike traditional cloud computing, which processes data in centralized data centers, edge computing brings computation closer to the source, on the factory floor, near machines, or at remote production sites.
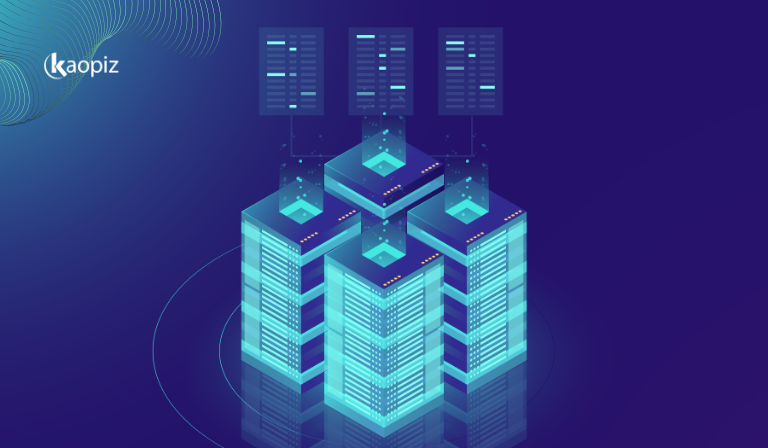
Edge computing will be one of the trends in manufacturing that plays a vital role in scenarios where speed, reliability, and responsiveness are mission-critical. For example, when AI-powered vision systems detect defects on a production line, decisions must be made in milliseconds to avoid costly downtime or quality issues.
Key benefits of edge computing in manufacturing include:
- Real-time monitoring and control of equipment and processes.
- Reduced data transmission costs and bandwidth usage.
- Improved system reliability, especially in remote or bandwidth-limited environments.
- Enhanced data security, as sensitive information can be processed and stored locally.
Rise of AI & Generative AI in Manufacturing
AI is one of the hottest IT trends in manufacturing industry that enables smarter, faster, and more adaptive operations. AI is not just a support tool, it’s a strategic driver across the entire production lifecycle, from design and prototyping to predictive maintenance and quality control.
Traditional AI applications like machine learning and computer vision are being widely adopted to monitor equipment health, forecast demand, optimize supply chains, and detect defects with greater accuracy than ever before. These intelligent systems are helping manufacturers reduce downtime, improve yield, and boost operational efficiency.
The spotlight, however, is increasingly shifting toward Generative AI – a groundbreaking development that takes automation and creativity to new heights. In manufacturing, generative AI is being used to:
- Automatically generate and simulate new product designs.
- Create production scenarios and test variables before physical implementation.
- Generate maintenance manuals, training content, and even intelligent chatbots for factory support.
Advanced Robotics and Human-Robot Collaboration
In 2025, the integration of advanced robotics and human-robot collaboration (HRC) is transforming the manufacturing floor into a more intelligent, agile, and safe environment. Robotics has moved beyond traditional automation to include flexible, AI-enhanced systems that can adapt to changing tasks, environments, and human interactions in real time.
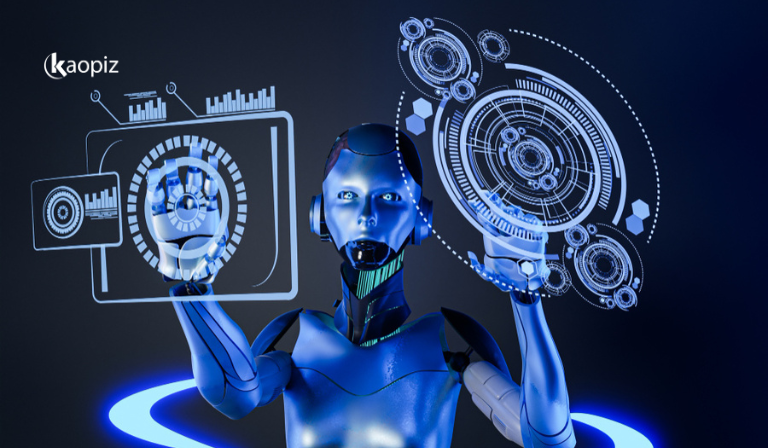
At the forefront of this shift are collaborative robots, or cobots, designed to work alongside human operators rather than replace them. Cobots are lightweight, cost-effective, and equipped with safety features such as force sensing and automatic shutdown when encountering resistance.
These characteristics make them ideal for tasks like:
- Precision assembly
- Material handling
- Quality inspection
- Packaging and palletizing
Human-robot collaboration also plays a vital role in addressing labor shortages. Instead of replacing workers, robots take over repetitive or hazardous tasks, allowing skilled employees to focus on higher-value responsibilities such as system monitoring, programming, and process optimization.
Digital Twins & Simulation Tech
Digital twins and simulation technologies are manufacturing IT trends that help manufacturers optimize operations, reduce risk, and accelerate innovation. A digital twin is a virtual replica of a physical asset, process, or system that mirrors real-world conditions in real time, powered by IoT sensors, AI, and cloud computing.
By simulating production lines, supply chains, or entire facilities, digital twins allow manufacturers to:
- Test different scenarios without disrupting actual operations.
- Predict failures and maintenance needs before they occur.
- Optimize processes for speed, cost, and energy consumption.
- Validate product designs and performance under various conditions.
This technology is especially valuable in complex or high-stakes environments where downtime is costly and safety is paramount. For instance, digital twins can simulate how machinery will perform under different workloads or environmental conditions, enabling predictive maintenance and minimizing equipment failure.
Decentralized Manufacturing
As global supply chains face increasing disruption from geopolitical tensions, natural disasters, and shifting consumer demands, decentralized manufacturing is emerging as one of the latest trends in manufacturing technology. Unlike traditional centralized models that rely on large, singular production hubs, decentralized manufacturing distributes operations across multiple smaller, tech-enabled facilities, often closer to end-users.
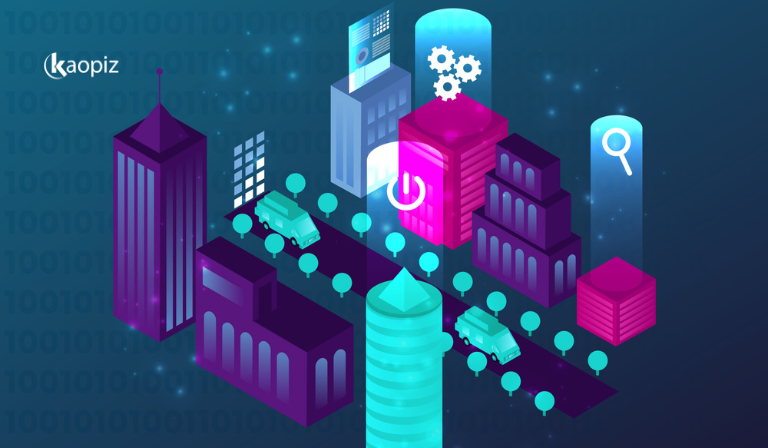
This model is made possible by advancements in cloud computing, IoT, additive manufacturing (3D printing), AI, and edge computing, which enable manufacturers to manage distributed operations efficiently and in real-time.
For example, manufacturers can 3D-print parts on demand in regional hubs or use real-time IoT data to coordinate production shifts across different facilities, eliminating delays and improving customer satisfaction.
Key benefits of decentralized manufacturing include:
- Faster response to market demand through localized production.
- Improved supply chain resilience and risk mitigation.
- Reduced logistics costs and carbon footprint.
- Customization at scale, tailored to regional preferences.
Decentralized manufacturing also supports sustainability goals, as it minimizes transportation-related emissions and allows companies to source and produce more locally.
Workforce Empowerment with AR/VR & Upskilling Tools
In 2025, Augmented Reality (AR) and Virtual Reality (VR) will become the new trends in manufacturing and reshape the workforce by providing immersive, hands-on experiences that dramatically improve training, collaboration, and equipment maintenance. These technologies are not just futuristic add-ons but practical tools driving real value on the factory floor.
AR/VR tools are becoming essential for employee training and upskilling, enabling workers to learn complex processes in a simulated environment without risking safety or slowing production. Whether it’s operating new machinery or assembling intricate parts, employees can practice tasks repeatedly, leading to faster learning curves and fewer errors on the job.
For product designers and engineers, AR and VR offer 3D visualization and prototyping capabilities, allowing teams to:
- Collaborate across locations in real-time
- Visualize product iterations before physical production
- Speed up innovation cycles with fewer design errors
Industries like automotive, aerospace, and heavy machinery are already seeing measurable improvements in quality control, assembly efficiency, and worker safety through AR/VR implementation.
Cybersecurity in Smart Factories
Cybersecurity is one of the manufacturing IT trends and a critical pillar of operational resilience. The rise of smart factories, connected devices, and cloud-based systems has made the industry a prime target for cyber threats. From ransomware attacks to IP theft, the risks are growing in both frequency and sophistication.

Manufacturers must invest in robust cybersecurity frameworks that safeguard both IT and OT environments to protect operations.
This includes:
- Conducting regular risk assessments and system audits.
- Implementing network segmentation and zero-trust architectures.
- Encrypting sensitive data and securing intellectual property.
- Deploying real-time threat detection and incident response tools.
- Training employees to recognize phishing, malware, and other cyber threats.
A key challenge lies in bridging the gap between legacy equipment and modern cybersecurity protocols. Many manufacturing systems were not originally designed with security in mind, making them vulnerable entry points if left unprotected.
Sustainability Through Green IT
In 2025, sustainability is a strategic priority for manufacturers, and technology is playing a critical role in achieving it. As companies face increasing pressure to reduce emissions, optimize resource usage, and meet environmental regulations, Green IT has emerged as a key enabler of eco-conscious manufacturing.
Green IT refers to the practice of designing, deploying, and using technology in ways that minimize environmental impact. This includes optimizing software systems, adopting cloud infrastructure, and leveraging intelligent tools that improve energy efficiency and reduce waste.
Key Benefits of Green IT in Manufacturing:
- Reduced energy consumption through smart resource allocation and real-time tracking.
- Lower carbon emissions by replacing energy-intensive on-premises systems with efficient cloud infrastructure.
- Minimized production waste via process optimization and predictive analytics.
- Improved compliance with global environmental standards and ESG goals.
For example, real-time monitoring tools help manufacturers track energy consumption, reduce raw material waste, and optimize production schedules. Cloud computing also contributes significantly, with Accenture estimating that cloud migration could cut carbon emissions by an amount equal to removing 22 million cars from the road.
Future Outlook: What’s Next Beyond 2025?
As manufacturing continues to evolve through 2025, the pace of innovation shows no signs of slowing down. Beyond this year, the next frontier of manufacturing software will be shaped by even more intelligent, autonomous, and sustainable technologies, driven by ongoing advancements in AI, quantum computing, and human-machine collaboration.
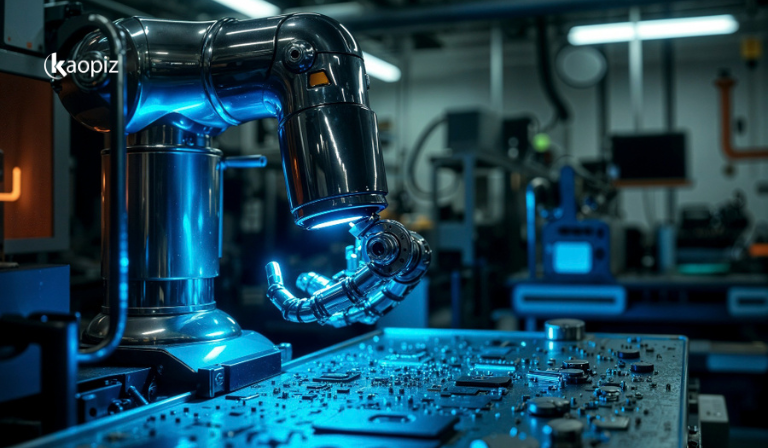
Key recent trends in manufacturing technology that are expected to define the post-2025 landscape include:
- Industry 5.0: Emphasizing human-centric, sustainable, and resilient manufacturing.
- Hyperautomation: Autonomous factories powered by AI, robotics, and edge computing.
- Quantum Computing: Unlocking complex simulations and supply chain optimization.
- Sustainable by Design: Green IT and circular manufacturing are becoming the norm.
- Immersive Technologies: Broader use of XR for training, design, and remote ops.
To stay competitive beyond 2025, manufacturers must remain agile and future-ready, embracing change, investing in innovation, and building digital infrastructures that can scale and adapt.
How Kaopiz Supports Smart Manufacturing
Kaopiz helps manufacturers embrace digital transformation and future-ready technologies to stay competitive in an increasingly connected world. Our customized IT solutions and advanced manufacturing technologies empower businesses to automate operations, improve decision-making, and accelerate innovation, all while maintaining cost efficiency and security.
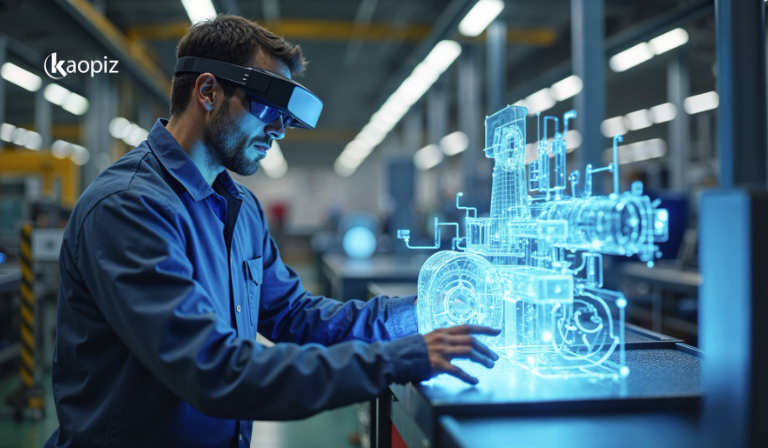
Our key services for the manufacturing sector include:
- AI & Machine Learning Solutions: Predictive maintenance, defect detection, process optimization, and demand forecasting.
- IoT & Edge Integration: Real-time data collection, monitoring, and control for smarter production lines.
- Cloud & DevOps Services: Scalable infrastructure, digital twins, and smart factory platforms.
- Custom Software Development: Tailored systems for workflow automation, resource planning, and analytics dashboards.
- Cybersecurity & Compliance: End-to-end protection of IT/OT environments and adherence to industry standards.
Whether you’re optimizing legacy systems or building a next-gen factory, Kaopiz combines deep industry knowledge with cutting-edge technology to deliver results that matter.
Conclusion
Embracing the latest IT manufacturing trends is no longer optional – it’s essential for staying competitive, resilient, and future-ready. From AI and edge computing to digital twins and green IT, 2025 is about leveraging smart technologies to drive efficiency, innovation, and sustainability.
By adopting these trends, manufacturers can not only optimize operations but also build more adaptive, customer-focused, and environmentally responsible businesses.
At Kaopiz, we’re committed to helping manufacturing companies navigate this transformation with tailored IT solutions that meet both today’s needs and tomorrow’s challenges.
Ready to future-proof your manufacturing operations? Get in touch with Kaopiz to explore how we can support your digital journey.
FAQs
What Are the Initial Costs of Implementing Smart Manufacturing Solutions?
The initial investment can vary depending on the size of the operation, existing infrastructure, and scope of the project. Costs typically include hardware (sensors, machines, devices), software (ERP, MES, AI tools), integration, and training. While upfront expenses can be significant, many companies see a strong ROI through increased efficiency, reduced downtime, and lower operational costs.
What Factors Should Manufacturers Consider When Choosing a Technology Solution Provider?
When selecting a provider, manufacturers should look for:
- Industry experience and domain knowledge
- Ability to deliver scalable, customized solutions
- Strong track record and client success stories
- Cybersecurity and compliance capabilities
- Ongoing support and system integration expertise
Partnering with the right provider like Kaopiz ensures smoother implementation, long-term reliability, and maximum value from your technology investment.
Should Small and Mid-sized Manufacturers Invest in Industry 4.0 Technologies?
Absolutely. Industry 4.0 is not just for large enterprises. Many modern solutions are modular, cost-effective, and scalable, making them accessible for small and mid-sized manufacturers. Investing in digital transformation can help them increase agility, compete more effectively, and future-proof their operations in a fast-changing market.
Trending Post
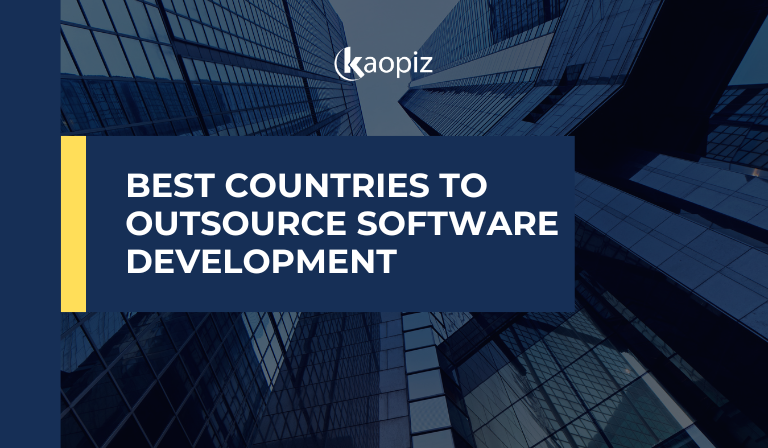


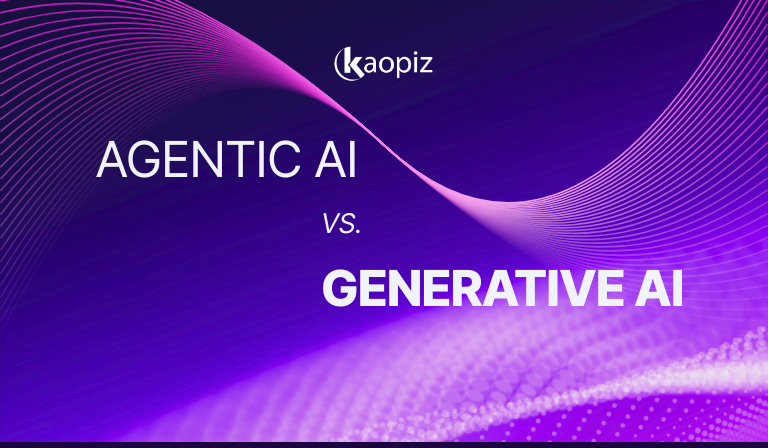